Komati Power Station
The Planning of Komati Power Station started during the mid-1950 on the farm Koornfontein. The deed of transfer of the land was signed on 22 November 1957. Site levelling started in April 1958 and the first unit, Unit 5, was commissioned on 6 November 1961 and Unit 9, the last, in March 1966.
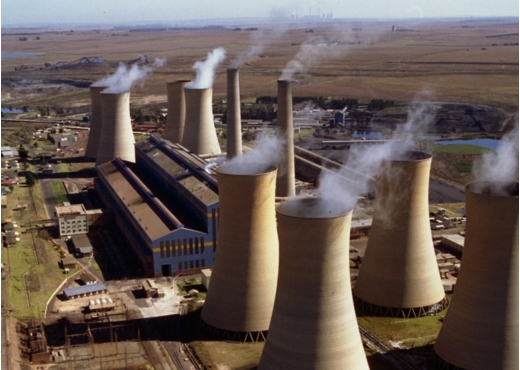
Komati power station is situated in the Eastern Transvaal (now Mpumalanga) halfway between Middelburg and Bethel, and when it was completed, it had a capacity of more than twice of any existing power station in South Africa at the time. Planning of this station commenced in June 1957. Its ultimate capacity was to be 1 000 kW produced by five generators (No’s 1 to 5) of 1000,000 kW each and four generators (No’s 6 to 9) of 125,000 kW each. Each generator has its own boiler. The first generator went to into service at the end of 1961, and the last machine was commissioned early in 1966.
The capital cost of the completed power station was estimated to be just over R80,000,000 of which about 80% was spent in South Africa.
A station of this size required a vast amount of fuel and water. For this reason it is situated next to two coal mines, the Koornfontein and Blinkpan Collieries. When completed the station would require up to 12,000 tons of coal per day and up to 18 000 000 gallons of water per day. Water is obtained from the Nooitgedacht Dam on the Komati River from where it is pumped to reservoirs at Klipfontein from whence it gravitates to the power station a total distance of about 40 miles.
Crushed coal from Koornfontein is mixed with water and pumped through a pipeline to the starting point of the overland conveyor near Blinkpan. Here it is dewatered and added to the output of the Blinkpan Colliery. The coal pumping plant has a capacity of 100 tons per hour. The main crushed coal supply came from Blinkpan Colliery. The overland conveyor is 1,817 feet long, has a capacity of 1 000 tons per hour, the belt being 42 inches wide and moving at 600 feet per minute, i.e. about 7 miles per hour.
The coal is delivered into two coal staithes which has a total capacity of 48 000 tons and from the staithes it is conveyed to the boiler bunkers.
Before the coal is fed into the boiler furnaces it is pulverized to a very fine powder in either tube and ball or ring and ball mills. The coal dust is then blown by means of heater air into the boiler furnace where combustion takes place. The furnace walls consist of steel tubes in which water is converted into steam. Boilers 1 to 5 can each convert 450 tons of water into steam per hour at a pressure of 1 250 lbs., per square inch and a temperature of 965ºF. The four larger boilers No’s 6 to 9 each convert 562.5 tons of water to steam at the same temperature and pressure per hour. About 85% of the available heat value of the coal is transferred to the steam in the boilers.
From the boilers the high temperature and pressure steam is passed to the turbines. As the steam passes through the turbine at high velocity it expands and gives up a part of its energy to the turbine rotor which drives the generator at 3,000 revolutions per minute. At the turbine exhaust end the steam temperature is only about 100°F and its pressure is about 12 lbs. per square inch below atmosphere, i.e. nearly that of a perfect vacuum. To attain this low temperature and pressure, on which the efficiency of the turbine largely depends, the steam has to be condensed at the low pressure and for this purpose a large quantity of cooling water is pumped through tube nests inside the condenser. The condensed steam is extracted from the condenser and after passing through various heaters is returned to the boiler for re-use.
A 100,000kW turbine requires about 4,000,000 gallons of cooling water per hour for its condenser. The temperature of this water is raised about 15°F while passing through the condenser and it has to be cooled again before it can be re-used. For this purpose, it is pumped into the cooling towers where it is cooled partially by evaporation and partially by warming the air that flows into the bottom and out of the top of the cooling towers. The cooling towers, which are 300 feet high and 202 feet diameter at the bottom, are large chimneys to create a draft of air, which cools the water. Water is sprayed into the bottom of these about 35 feet above the pond. The major part of the 18,000,000 gallons required by the station per day is to make for water lost by evaporation in the cooling towers.
Coupled to the turbine shaft is the rotor of the generator. In the generator the mechanical energy of the turbine is converted into electrical energy. The generators are sealed and filled with hydrogen gas as a cooling medium. Hydrogen is used because it is a good conductor of heat and also being a very light has the friction losses in it are very much less than would be the case if air was used.
The generator output of about 6,000 amperes at 10,5000 volts conveyed through heavy aluminum conductors to the generator transformer where its voltage is stepped up to 300,000 volts, and from where it is connected through high speed air blast circuit breakers to the 300 kV bus bars in the high voltage yard. Also connected to these bus bars through their own circuit breakers are the transmission lines, which interconnect Komati power station with Eskom’s high voltage transmission system.
The operation of much of the equipment described is automatic requiring complicated control and protection equipment as seen in the boiler and turbine control panels and in the switch operating room and many other places all with their attendants and operators. Then there are the maintenance and repair workshops and comprehensive stores for spares and consumables, chemical plants for water purification and a multitude of other services.
The employees who control and operate the station live in the power station village. When the station was complete there was about 200 European and 300 Black employees. For the Europeans there were 196 dwellings in addition to single quarters which provided for about 80 men. Part of the single quarters was allocated to temporary maintenance and repaid staff. There is a modern compound for 300 Bantu employees and 7 married quarters.
Recreation facilities were provided comprising tennis courts, rugby, cricket and soccer fields, jukskei, swimming bath and recreation hall. The school had 300 pupils. Merchants from Witbank, Middelburg and Bethal called at frequent intervals with merchandise and provisions.
Komati power station is currently being brought back to service after a mothballed period of approximately 16 years.
In November 2004 a decision was taken to reinstate the station as one of the “Return to Service” sites.
Komati has nine generating units with a total installed capacity of 1 000MW.
5 X 100 MW units and 4 x 125 MW. The sent out capacity is 961MW.
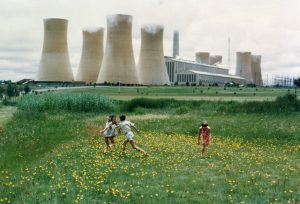
Operational life of the individual units is expected to be 15 years from its date of return to Commercial Operation, with a total of 20 years for the station. Annual plant load factor is expected to be in the range of 45% to 90%.
Refurbishment of Komati power station will allow the plant to supply reliable power in a “load following mode, but Komati could well be called upon to “base-load” when required.
Mothballing of Komati
During the mid-80’s a decision was made to take out units and later the entire Power Station was out of service, mainly because of the following reasons:
- Surplus capacity
- Increasing maintenance costs of the older plant
- To be able to put newly built power stations, such as Majuba, in commercial service and make use of the guarantee period.
Return to service
It was also decided not to let the plant deteriorate but to conserve it properly to return it at a later stage. The conservation process was called mothballing. The first plant to be mothballed was Turbine 5 on 15 December 1987 followed by Boiler 3 on 26 March 26. The rest of the plant was mothballed at intervals thereafter and the last to be mothballed was Unit 4 on 06 December 1990. Different methods were used to prevent deterioration of the plant, such as painting, the use of vapour corrosion inhibitors (VCI) and the passing of dehumidified air through the boilers, turbine feed and steam circuits and the generators. Komati Power Station reached a huge landmark on the 9th of February 2012 with 6 units on load for the first time since 5 October 1989. Calculated, this means having 6 units available after 22 years, 3 months and 4 days. In the early 2000’s a decision was taken to return Komati Power Station to service to meet the growing demand of electricity.
The User Requirement Specification was compiled and approved on 14 August 2006. The units were returned to service starting with unit 9; this unit was declared fit for Commercial Operation on the 24th of December 2008. Unit 8 followed on 1st of March 2009. With a goal of being the “Best return To Service Power Station By Far” and a motto of “We are Powered by Performance”, Komati won most of the winter challenge awards for 2010.
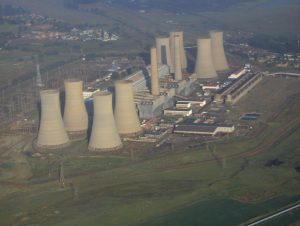
This proved that Komati is not only the best Return to service Station by far but the best in Production Unit Coal 3. Komati ended up TOP in Plant Performance in 2010. Komati set a new goal in 2010 to “Be the Best of the Best in Generation” More than a year later unit 7 was declared fit for Commercial Operation on the 12th of July 2010. Unit 4 followed on 29 December 2011 and unit 5 on 3 February 2012. Unit 6 has not yet been declared Commercial but this will follow soon. By the close of 2012 Komati will have 9 units running with a total generation capacity of 1000 MW.
Technical Details
Komati was one of the first pulverised fuel firing stations and designed to generate 1000 MW with five units rated at 100 MW and four at 125 MW
- Five 100 MW Units
- Four 125 MW Units
- Installed capacity: 1000 MW
- Design efficiency of rated turbine MCR (%): 30.00%