Nuclear Safety and Licensing
Emergency Planning
Public Safety Information Forum (PSIF) Minutes
Radioactive Waste
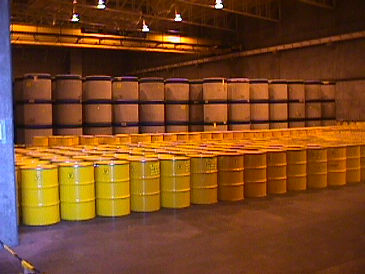
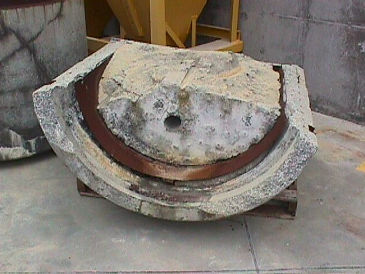
Intermediate Level Waste
Intermediate level waste consists of purification sludges, spent resins, filter cartridges and irradiated scrap metal. This waste is more radioactive than the refuse but less radioactive than spent fuel. It is mixed in a very specific way with concrete and sealed into appropriately marked concrete drums. These drums also go to Vaalputs.
The concrete is constituted in such a way that even if a drum fell off a truck or broke open the radioactive materials inside could not harm the public because it has been sealed inside the concrete and cannot escape.
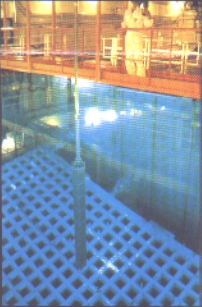
What is high level waste?
High level waste is fuel that has been used in the fission process. It is radioactively extremely dangerous. When it is removed from the reactor vessel it is stored in special “fuel pools”.
After ten years in a fuel pool it is “cool” enough to be moved into thick-walled casks which can be stored above ground for up to 40 years. Ten years has been chosen because in that period the bulk of the radioactivity from the short lived nuclides has decayed. This is known as dry storage and also interim storage.
A two-reactor pressure water reactor power station like Koeberg generates approximately 32 tons of spent fuel for both units each year. If one adds the metal from the fuel assembly structure this would be 47 tonnes / year (fuel + fuel assembly structure). Over a 40-year period this translates into 2729 used fuel assemblies stored on site (1255 tonnes of used fuel and 1828 tonnes including fuel assembly structure).
Each spent fuel assembly contains radioactive materials which fall into three categories.
The first category contains the fission products (such as caesium, iodine, strontium, and xenon) which are created when uranium or plutonium nuclei are split. They are the most radioactive components of spent fuel when it leaves the reactor vessel for the fuel pool but they decay to low levels relatively quickly and after 1 000 years only about 400 GBq of the longest-lived fission products such as iodine 129, remain.
In the second category are the actinides, which are isotopes of uranium and heavier metals including plutonium. These are long-lived materials which take 10 000 years to decay to about 800 GBq.
The last category contains the structural materials of the fuel assemblies which become radioactive through irradiation by neutrons. They only add a small amount of radiation to the whole spent fuel assembly total and decay in about 500 years to less than 200 GBq.
How quickly does the radioactivity decay?
A remarkable feature of spent fuel is that after one year of storage only 0.92% of the radioactivity remains in the assembly because the radioactive nuclides in the material decay so quickly.
After 10 years, which is the earliest time at which the assemblies would be taken out of the fuel pool, only 1% of the original radioactivity remains.
What is left after 10 000 years of storage is about 0,0002% of the radioactive content and most of that would be plutonium and other actinides. After this period the radioactivity has decayed to below what would have been there had the uranium been left undisturbed in the ground.
Radioactivity decays until it is harmless. In other words, spent fuel eventually gets rid of its own toxicity – unlike chemical toxic waste, which must be pro-actively treated to make it harmless.
Spent fuel
Eskom has, since it began operating, looked at various options for storing it’s spent fuel.
The station when built was a copy of a French Pressurised Water Reactor (PWR). As such the station was originally designed to store spent fuel on site for only 5 years whereafter the fuel would be sent off for reprocessing. This process was and remains a very expensive option. During the late 1980’s the fuel pools were re-racked in order to store fuel for a 10 – 15 year period. This was state of the art technology at the time.
The fuel pools at Koeberg soon reached capacity in 2000 and so Koeberg installed super high-density racks. This new technology enabled the storage of spent fuel for another 20 years (around 1326 used fuel assemblies per unit, with another 210 storage positions for a core unload).
Given that the spent fuel pools have reached capacity, Koeberg has started storing used fuel in dry storage casks on site which is common practise internationally and a robust method of used fuel storage. The figure below shows the increase in stored fuel on site over time. The figure is conservative as it assumes that low burnup fuel will be chequerboarded in the spent fuel pools resulting in less fuel storage in the pools over time.

The current casks in use at Koeberg weigh more than 90 tonnes and are made of steel. In future concrete casks might also be used.
The casks have thick walls to:
- Providing strength needed for the cask wall;
- Providing shielding from the radiation emitted by the spent fuel; and
- Be safe and manageable for transportation.
The cask is also designed so that the remaining thermal heat in the fuel assemblies is dissipated naturally. The advantage of this is that no heat removal systems which will require monitoring or maintenance are necessary. The heat losses occur in the same way as it does when a cup of tea is allowed to cool down.
The casks are tested to cover three areas:
- The structural ability of the cask to withstand strains caused by the use for which it is intended;
- The durability of the materials; and
- The performance of the cask under unexpected or accident conditions.
Prototypes of the Koeberg casks have been dropped at various angles from a height of nine metres to see whether they broke or developed cracks through which fuel or radioactivity could escape. They remained sound.
In the UK, similar casks have been smashed into by a train locomotive traveling at a speed of around 160kms/hr without compromising safety.
Power station operators have a choice regarding the decommissioning costs they incur. They can decommission the entire station soon after shutdown and accept the cost of dealing with highly radioactive material. Or they can dismantle the non-radioactive parts of the site buildings immediately and leave the central block around the reactor itself for perhaps 50 years and accept the cost of maintaining it for that period. Eskom has opted for immediate decommissioning of the central block so as to not burden future generations with the waste.
There are nuclear stations that have been shut down and decommissioned throughout the world . All decommissioning activities are supervised by independent nuclear safety authorities. In South Africa’s case this authority would be the National Nuclear Regulator . They establish safety requirements for the decommissioning workers and the public and ensure that they are adhered to. Great care is taken to prevent the spread of possible radioactive dust and liquid effluents.
All organisation operating nuclear stations including Eskom are obliged to set aside funds to cover eventual decommissioning. These funds are set aside from the profit generated by the power station itself.
The options for Koeberg as far as decommissioning is concerned are:
- It can be shut down, sealed and left under close security for as long as its reactor systems inside the containment buildings are radioactive.
- It can be shut down and the containment buildings filled with concrete to prevent any radioactivity present in the buildings from escaping.
- Under the Greenfield Option the Koeberg site can be rehabilitated to be left exactly as it was before the power station was built. This could only be done if the two radioactive cores and containment buildings were cut up and put into containers and buried, along with the waste and spent fuel.
- After removal of the radioactive components the site could be used for another nuclear power station or a conventional power station.
- It could be used as an industrial complex as it has all the infrastructure.